
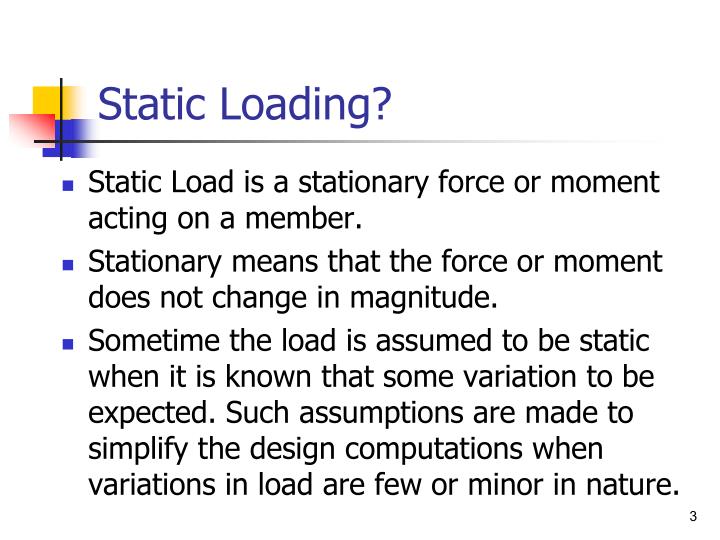
It has an intuitive graphical user interface, making it easy to set-up and run.
#Static loading windows
The Controller employs industry-standard hardware for easy upgrades and runs on the Windows operating system.
#Static loading software
The MTS FlexTest Controller is a reconfigurable load control system that can conduct both static and fatigue test programs using the latest in structural test control software and algorithms. Load control for fatigue applications is typically accomplished using cyber computer-controlled servo feedback control systems, or one of our new MTS 140-Channel FlexTest Structural Test Controllers. We can also perform comparison fatigue testing of OEM and alternate source parts to demonstrate the equivalency of fatigue life.ĭTB utilizes servo-controlled linear or rotary hydraulic actuators to apply the test loads or displacements during all static and fatigue testing.
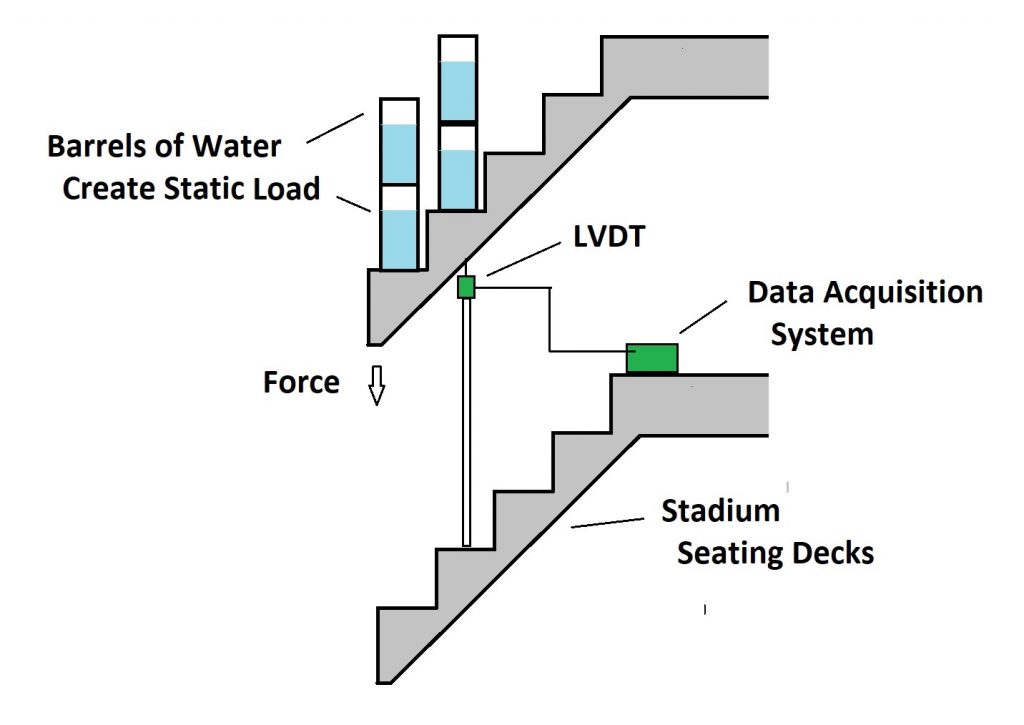
We are able to apply linear or angular displacements utilizing linear and rotary hydraulic actuators. Our centralized hydraulic power unit supplies 800 GPM of hydraulic fluid at 3,000 PSI pressure.ĭTB performs constant amplitude or spectrum fatigue loading of components up to 400 KIP, at frequencies up to 25 Hz (depending on load and displacement requirements). We also have the engineering resources and design talent available to design and fabricate specialized test fixtures to test any type of component that requires fatigue testing. Over 100 major test fixtures are available to test specific aircraft components. If you have simulated or recorded field data, we can work with you to “truncate” the spectrum and weed out the conditions that do not affect the component’s fatigue life.ĭTB’s well-equipped test laboratory is capable of performing coupon, component, and full-scale fatigue testing.
#Static loading full
If fatigue load testing is required using statistical methods, a loading spectrum can be determined that consolidates the recorded data into the full range of conditions. If required, we can also conduct testing to failure to measure the structural breaking point of the article under test. Static load tests can be performed to loads that are a fraction of the designed limit load, but may also be tested to the ultimate limit, which is typically much higher than any load that the article would encounter in the real world. Dimensional inspections can be conducted to quantify any permanent deflections by comparing pre-static loading to post-static loading. During the static load test, data is continuously recorded with data “snapshots,” which are taken at prescribed loading increments. Load cases are then developed to simulate critical conditions.
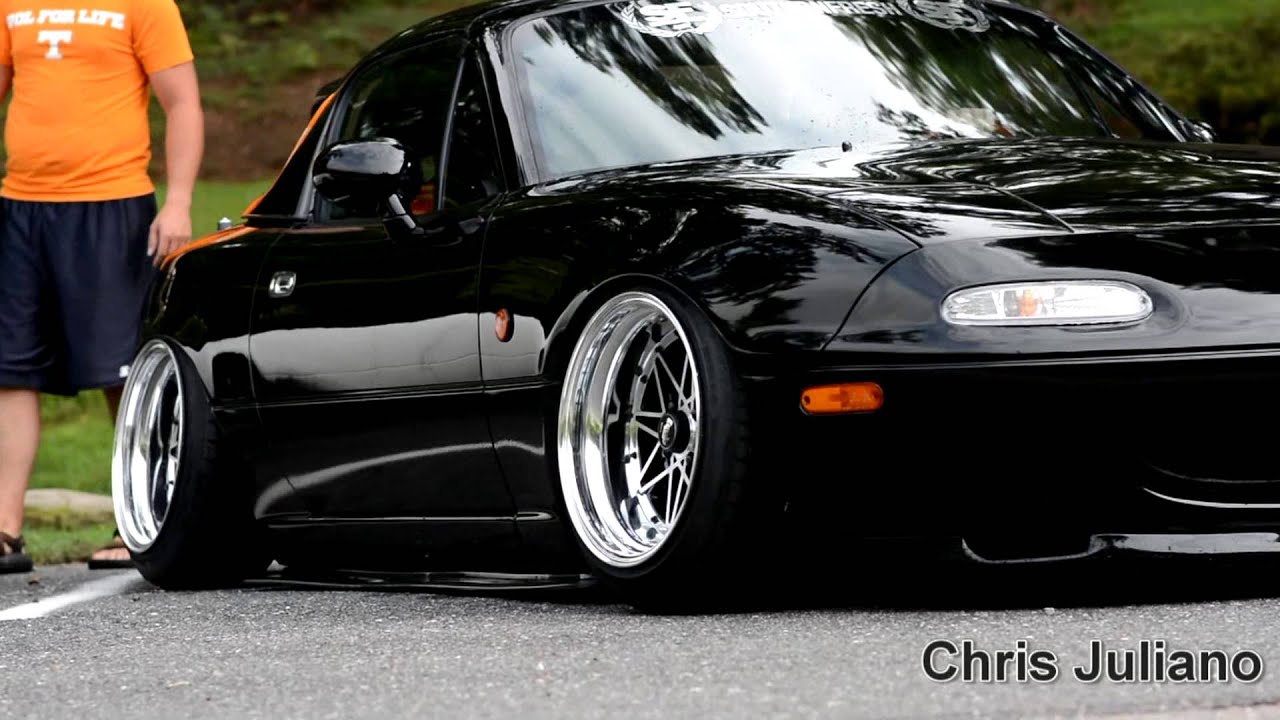
The test article, which can be anything from an aircraft wing to a full plane, is placed in the fixture and outfitted with data acquisition equipment. At DTB, this type of testing generally utilizes large test fixtures that are designed to handle the strength and rigidity requirements that occur when applying loads. Static load tests are conducted in order to determine a test article’s ability to handle loads.
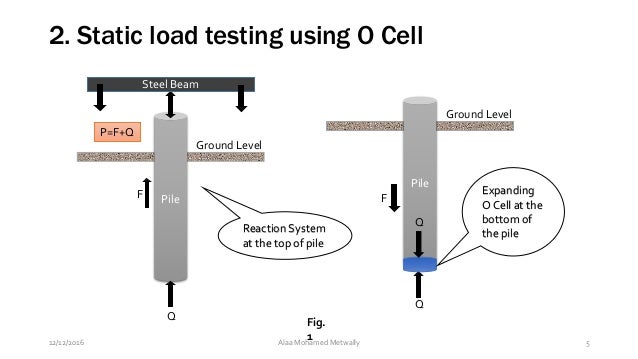
Plating, Coating, & Surface Evaluations.Macro- & Micro-Fractographic Characterization.Combined Environment (Temp / Alt / Hum).
